Why to remove oxygen from Olefin (ethylene or propylene)?
Polyolefins –polyethylene(PE) and polypropylene(PP), are very important industrial products, which are obtained by the polymerization of ethylene or propylene over a catalyst.
The presence of trace amount of oxygen during the olefin polymerization reaction can destroy the active center of the catalyst, and the participation of oxygen in the polymerization reaction reduces the directional conversion ability of the polymerization catalyst to generate oxygen-containing random active chains.
As a result, not only will reduce the selectivity, activity and conversion rate of the polymerization catalyst, but it will also affect the physical properties of the polymer, and may even lead to production stoppages and shutdowns, making the plant less productive and economically efficient.
Therefore, polymerization catalyst requires less than 0.10 ppm of trace oxygen in olefins. So how to deeply remove oxygen from olefins?
1, Oxygen removal from ethylene –Pd catalyst
Palladium catalyst is a deoxidizer using palladium, a precious metal, as the active component.
Taking oxygen removal from ethylene from FCC dry gas as an example, a typical oxygen removal process flow is as follows:
- The gas source entering the deoxygenation system is the gas after the PSA purification, the oxygen content of the gas is 300-900 ppm.
- Before entering the reactor, the gas is purified and the hydrogen sulfide is removed to below 0.1 ppm,
- then heated to 200 ℃ and fed into the deoxygenator from the upper part.
- Under the action of catalyst, the oxygen and hydrogen in the gas react to produce water.
- Oxygen content after treatment is less than 1ppm.
In this process, there are three main reactions :
1 H2+O2=H2O
2 CH2=CH2+H2=CH3-CH3
3 olefin cracking produces carbon accumulation
The latter two are side reactions.
The oxygen removal process requires a high selectivity of the catalyst in order to ensure a smooth oxygen removal reaction at low temperatures.
The increase in temperature is beneficial to the oxygen removal reaction, but the life time of the catalyst will be shortened at high temperature. In the dry gas extraction process, the temperature is set at 250°C. The hydrogen and oxygen content in the gas mixture entering the oxygen removal reactor are controlled to be below 1.5% and 0.1%, respectively, to ensure the accuracy of oxygen removal and longer service life of the catalyst.
After a long period of operation, the catalyst bed will be contaminated and the carbon accumulation on the surface of the catalyst will increase slightly. Controlling the bed temperature is the most effective way to extend the catalyst life.
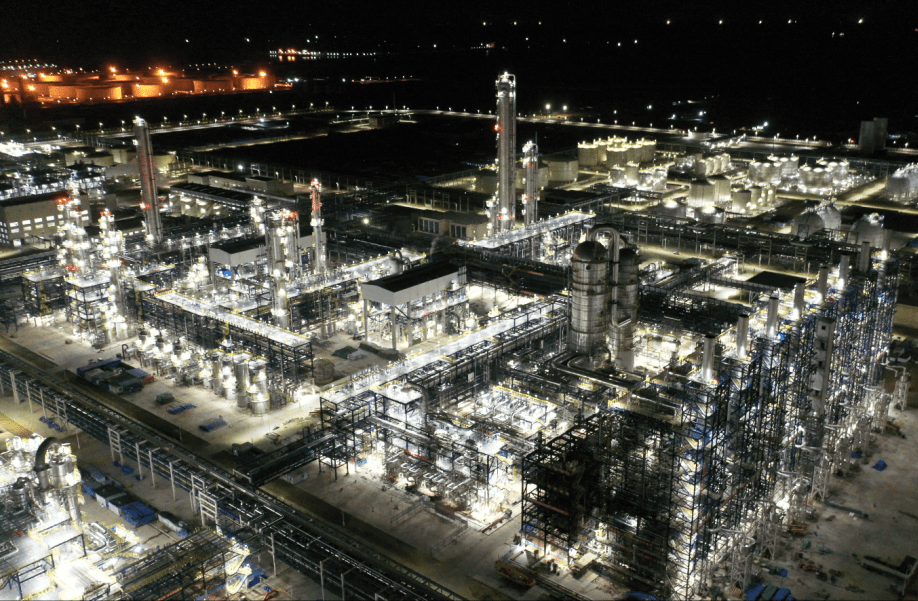
2 Oxygen removal from ethylene —Mn(Manganese) based catalyst
Another main catalyst for Oxygen removal from ethylene is Mn based deoxidizer.
Mn based deoxidizer is mainly used for Oxygen removal from ethylene in polyethylene production processes.
Manganese is an easily redoxable metal and allows for easy activation and regeneration of the catalyst. In the preparation process, suitable additives are added and scientific process is carried out to make the catalyst with deep Oxygen removal depth, high oxygen capacity, high mechanical strength, and not easy to occur side reactions. The operating temperature is room temperature to 200 ℃, space velocity is 5000-10000h-1, oxygen capacity > 15ml/g and oxygen content could be as low as 0.01ppm after treatment.
Mn based deoxidizer also can be used for oxygen removal from nitrogen, hydrogen and inert gas.
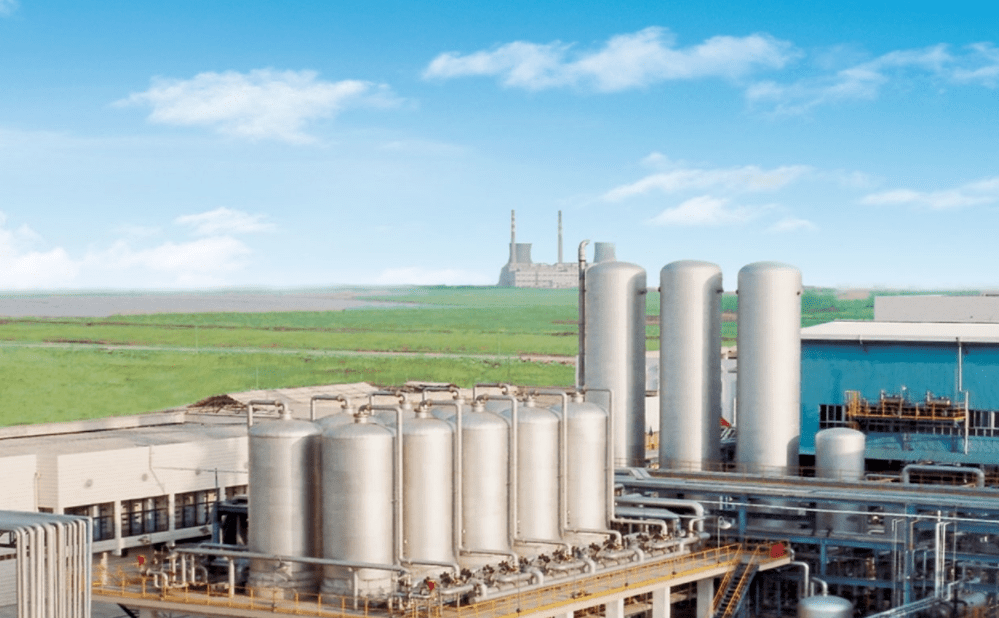
3, Oxygen removal from propene
Mn based deoxidizer is also used in the process of oxygen removal from propylene, replacing nickel catalyst , overcoming the problem of “temperature runaway”. Its reaction and activation/regeneration mechanism are as follows
- oxygen removal reaction: MnOx+nO2→MnOx+n+Q
- activation (regeneration) reaction : MnOx + 2n + nH2 → MnOX + nH2O + Q
The appearance of Mn based deoxidizer is brown-black bead with good oxygen removal performance. The operating temperature is between room temperature and 120℃. The maximum space velocity can reach 6000h-1. The oxygen in the raw gas can be removed to below 0.1ppm.
4, Conclusion:
Mn based deoxidizer is the most commonly used olefin deoxidizer with high oxygen capacity, not easy to sinter and low cost, but its reduction and regeneration temperature is 170-350°C, which is more than 20°C higher than Cu based deoxidizer and Ni based deoxidizer.